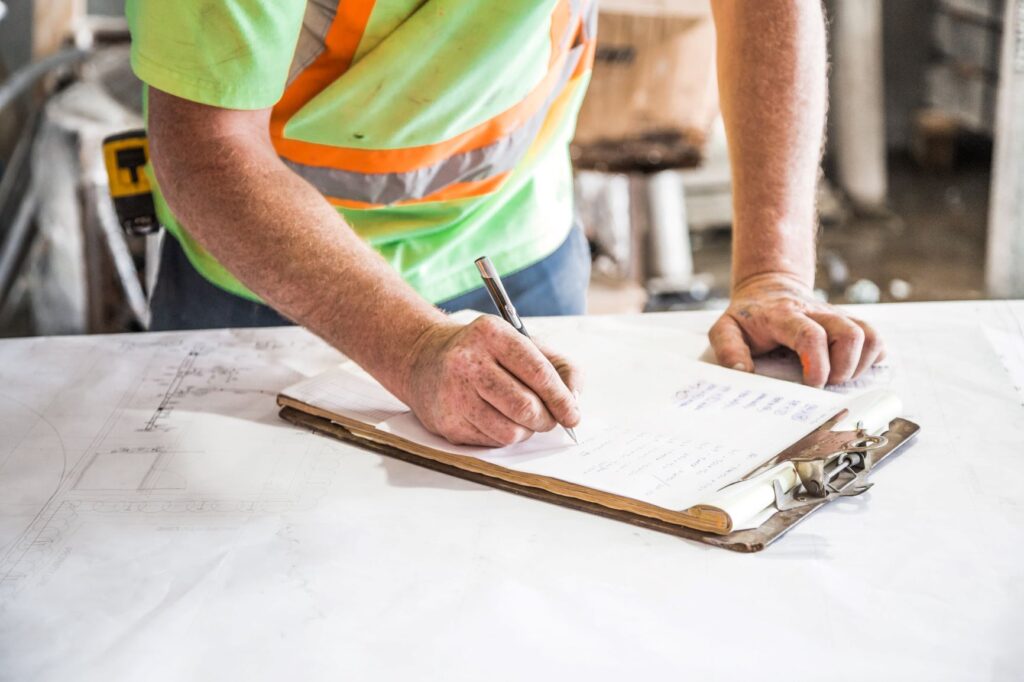
To conduct a quality inspection will bring you many benefits. This will allow you to avoid many problems in the future such as selling defective products, over expenses of the claim, wasting time, and many more issues just cause by a low-quality product. As a buyer, you need assurance from your supplier that your orders meet all of your standards.
A pre-shipment product inspection is the last chance for you to ensure your product quality. And then the next question is, what you should do if your inspector found many defects?
According to AQL (Acceptable Quality Level), there are three kinds of defects, as follows:
Minor defects: A small defect which has not much influence on the product. Furthermore, this defect is not lessening the function of the product. Some consumers will still buy such products. The AQL for minor defects is 4%.
Major defects: This defect is affecting the product both in appearance and function. This defect is usually not acceptable by the end-users. This defect would likely cause a customer to return the product, complain, or request a refund in response. The AQL for major defects is 2.5%.
Critical defects: This is the most serious defect, the product with a critical defect could harm the consumer. This defect could put your businesses at serious risk of product liability issues, lawsuits, and product recall. Such defects are unacceptable. Critical defects are defined as 0% in AQL.
Several common issues usually found during the pre-shipment inspection are:
- Low quality, where the quality of the product is far from the approved sample provided by the supplier.
- Missing quantity, when the number of goods reported does not match the actual number of goods packed for shipping.
- Wrong labeling, putting the wrong label on a product can cause misleading.
- Bad packaging, which can threaten the product’s safety.
A major defect that influences the appearance of the product. A major defect on a furniture inspection.
Bad packaging can threaten the product. A low-quality product that can affect your company’s reputation.
What do you need to do if the inspection is failed?
Failed inspection commonly happens when you are importing goods; therefore as a buyer, you should always have a second, third, or even fifth plan to anticipate the worst situation that might happen. Here what you can do after the inspection is failed:
1. To evaluate the importance of the quality issues
First of all, you need to understand the problem. Why does the inspection failed? Are the defects classified into minor, major, or critical defects?
2. To prepare the action plan
After you have understood the issues, your product is not of the quality you expected. Usually, there are several things you can do, such as refusing the good, getting a discount and shipping the goods, or sorting out the defects and reworking the goods.
3. Conduct Defective Product Sorting
If you want your supplier to rework your product, The Defective Product Sorting inspection is the only way to verify that your supplier has properly reworked the products to ensure a non-defective shipment. This inspection focused to ensure that approved products are sorted out from rejected ones.
What do we do in this inspection?
- Focus on sorting out any defective products
- Establish record and statistics about known defects
- Negotiate with vendor based on quality issues
- Ensure the factory correctly reworks the goods
- Refuse shipment of defective products
Excellencial third-party Defective Product Sorting in Indonesia will help you to eradicate defective goods from your supplier’s production and increase your brand image.